Arbutus West Agency Ltd.
Enhancing Our Clients'
Value Proposition With Industry Expert Application
At Arbutus West, our primary goal is ensuring our clients receive the utmost power quality, that is delivered efficiently, cost-effectively and reliably. Electrical systems are becoming increasingly complex and it is our job to provide expert analysis and solutions for your unique needs. In these case studies you will see how Arbutus West, along with our sister company Acacia Power Solutions, has been able to assess power supply problems, diagnose the problems and provide long-term solutions.
Load Bank Testing
Sector: Mining & Exploration
While testing a 2000 kW diesel generator, PowerLens™, Acacia’s proprietary software tool developed by power engineers for the specific purpose of analyzing, commissioning, and troubleshooting power systems, captured a peak transient of 964 V.
This represented 246% of rated voltage suddenly appearing in the system. After further investigation, the source of the problem was the opening of the main generator breaker to the load bank before all the cooling fans were shut off. The generator breaker interrupted the inductive current to the fans and this sudden change caused the inductive reactance of the motors to try and maintain the inductive current flow.
Thus, a switching procedure created a damaging voltage that could fail motors and/or other equipment in the system. A simple operational procedure change was the solution: first remove all fans from service before opening the main generator breaker.
Static Var Compensator Commissioning
Sector: Theme Parks
In many cases, sophisticated power equipment is not set to run “as-is” after installation and proper commissioning and troubleshooting can be needed to get equipment operating properly.
Theme parks are constantly in search of new and intense thrill rides, and with this often comes even greater power requirements.
In this case study, Acacia’s simulation work determined a ride’s reactive power requirement was too great and necessitated a static var compensator (i.e. real-time var compensation) to keep the ride from creating excessive voltage flicker across the power distribution system.
After installation, Acacia monitored the equipment to ensure it was providing the specified vars within the specified time response.
Due to the fast load and unload profile of the ride, the static var needed to operate in an open-loop control mode, matching var for var to create a net unity power factor load. During commissioning it was discovered the response was inadequate and the source inverter modules were producing excessive harmonics. Vendor investigation uncovered a need for significant updates in the controls and logic. Unfortunately, that initial update caused a failure in the static var which blew all fuses on the input. Powerlens™ real-time captured waveforms of the fault allowing the vendor’s engineer to quickly determine the problem’s source and implement an effective solution.
Harmonic Mitigating Transformer
Sector: Telecom
Equipment over-specification – you may not need what you think you need.
A client was placing an order for a harmonic mitigating transformer to feed rectifiers in a Telecom application and asked for help specifying the type.
After discussions regarding the particular rectifier, it became apparent that its harmonic signature was unknown. Also, a harmonic mitigating transformer had been specified, thinking it would cover for any harmonics.
This is an unfortunate over-specification response which often happens when specifications are reused. Many engineers are unaware that “harmonic mitigating” is, in actuality, a broad term for a host of transformer designs used with varying performance and application methods.
It was clear, then, that further analysis of the load and the application was essential in order to properly specify the client’s transformer. At this point, by our request, the client supplied a sample rectifier that was evaluated for harmonic content under its expected modes of operation.
Surprisingly, results of the measurements showed that a harmonic mitigating transformer was not even needed in this application. The rectifier utilizes source inverter electronics and produces relatively low levels of problematic harmonics as shown in Figure 3.
From the spectral analysis and additional calculations, it was determined that a K-Factor of 2 would be needed to allow full-load operation in the presence of the rectifier’s low-level harmonics.
The analysis also showed that high-frequency noise from the rectifier (as shown below) was present at all times. Thus, in addition to the K-Factor rating, shielded cables were specified along with an Environmental Potentials EP2000 to absorb the noise.
Finally, a lower- cost standard transformer (much less expensive than a harmonic mitigating unit) was specified as noted and ordered. This analysis not only helped supply the correct equipment and save money, but increased client confidence by knowing that the installation would fully meet the needs of the application.
Mysterious Feeder Faults
Sector: Petroleum & Chemical
Equipment over-specification – you may not need what you think you need.
An oil pumping station utilized a long overhead feeder to transfer prime power generation from diesel generators to a pumping station. This line had a series of mysterious faults and subsequent trips with no apparent cause.
To investigate this issue, instrumentation was set to capture faults at one end of the line. After capturing the first fault (see figure below), data was analyzed to determine the fault location on the feeder. That location was inspected and again yielded no conclusion of the cause. After capturing 4 to 5 faults, evaluating the fault location and performing multiple inspections, still no root cause had surfaced.
This led to recommending hiring locals to literally stand in several locations along the line and visually monitor the line until another fault occurred. From this action, one of the acute locals noticed insect activity on the line where wasps were building mud nests on the insulators.
As shown in the figure below, this mud contamination covered significant insulator creep. It would have been just a matter of time until this mud nest would flashover on the insulator. After any flashover and fault for this issue, it is clear that the mud nest would have been vaporized leaving no indication of a problem.
There is no solution that can control the nest building activities of these insects. Any material added to the insulator would compromise its insulating capability.
The best and only option was replacing the overhead line with an underground cable.
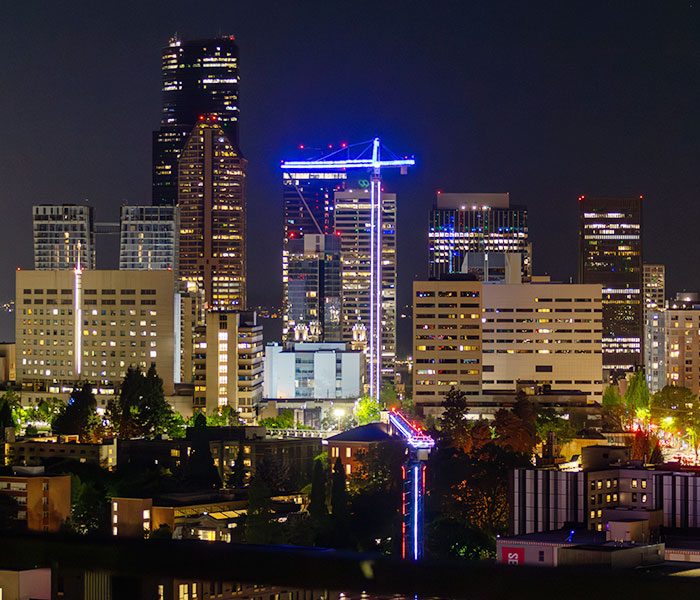
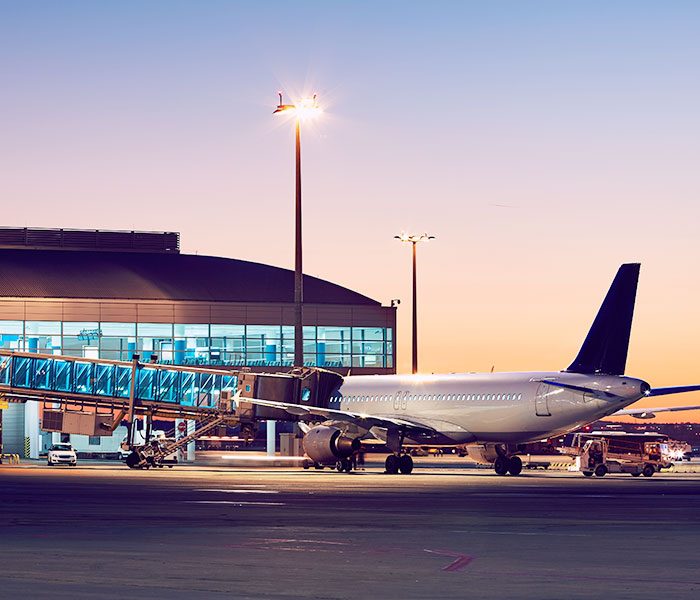
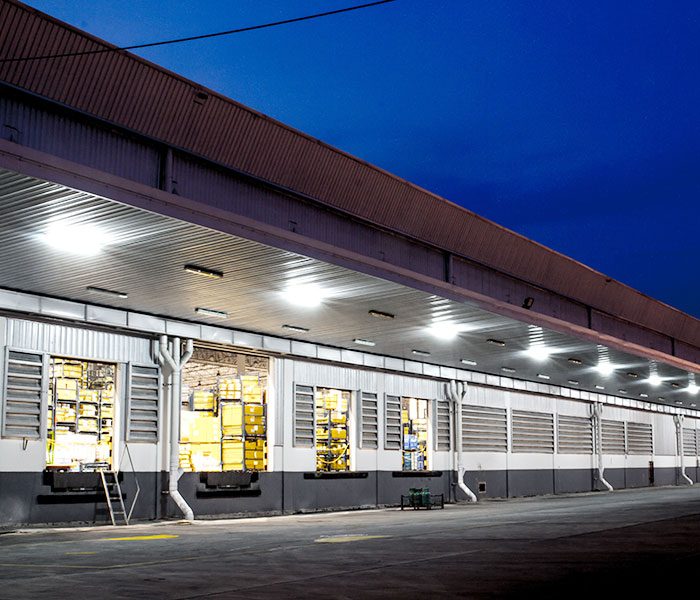
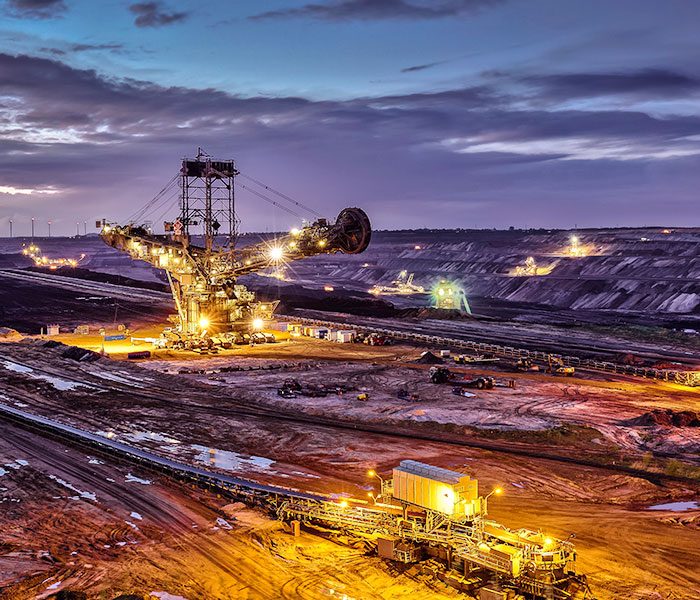
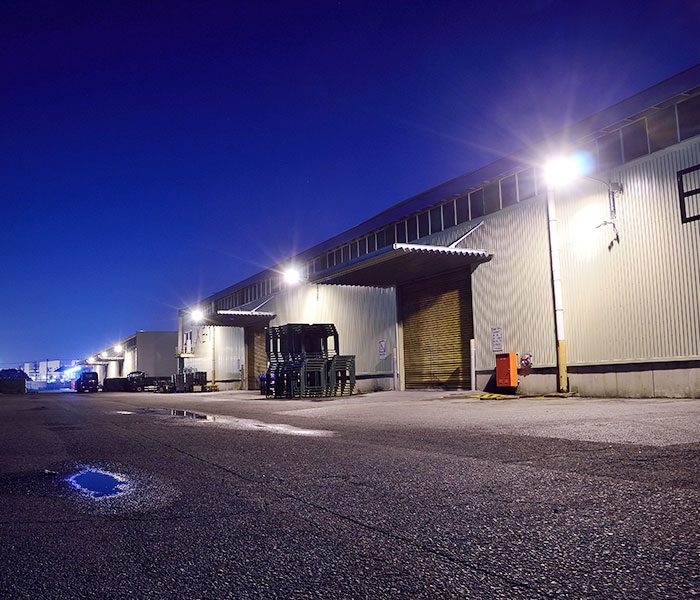
Arbutus West Agency Ltd.
Backed By
Industry Expertise
Expert-driven strategies to maximize efficiency and solve problems before they arise.
Backed by 30+ years of industry expertise, we specialize in uncovering the unique needs of your power systems. Leveraging advanced technology, we diagnose inefficiencies, address root issues, and prevent future disruptions.